火红的七月,锻造车间干部职工战高温、斗酷暑,以“心往一处想、劲往一处使”的精气神投入到生产经营中,万吨压机单月产量实现3178吨,标志着该车间产量迎来一个新突破,开创了自2012年万吨项目投产以来月产量历史新高。这不仅为锻造车间下半年高效生产开了好头,更为锻造万吨车间以后的提产保质树立了全新的标杆。
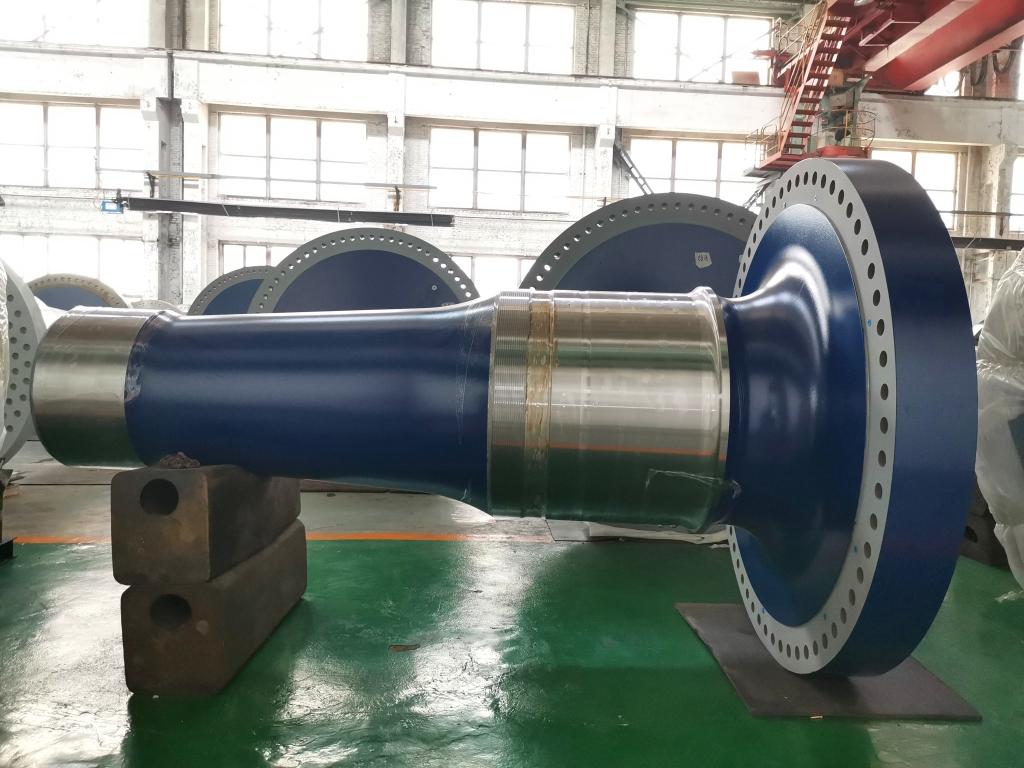
月初,分公司提出了月产量3000吨的目标。为实现目标,分公司紧紧把握订单增量与原材料供应充足的利好条件,多次召开会议进行精细排产和生产组织;生产过程中,想方设法保障设备高效运行,加强技术服务,增加炉窑装炉量,缩短更换工装辅具时间,全方位提高生产效率和运行质量。
全员立足岗位、勇挑重担。万吨压机启动后,满载红料的台车炉驶出,技术、生产、设备等人员全部深入一线,投入到紧张的生产中。在中午室外温度35℃、车间内温度接近50℃的情况下,职工手持对讲机与压机司机实时沟通、行车工忙着倒运物料、锻工手持样杆测量近千摄氏度产品尺寸、钳工实时监控设备运转情况.......所有人严格遵守各项质量管控流程,忙碌的身影遍布在车间各个角落。为确保产量,职工们轮流吃饭、休息,做到人休机不停,夜班,行车工需要将第二天的钢锭装炉、锻工将现场氧化皮清铲完毕。机器轰鸣声不绝于耳、职工作业忙而有序,与生产各环节配合无间,构成了一幅火热的高产画面。
设备保障是高产的前提。为保证连续生产与降低能耗,做好强有力的后方支持保障,维修小组与生产小组及时沟通,利用不同产品使用设备不同的差异性,在不影响火次生产的前提下对主要设备进行预检预修,积极消除现场“跑、冒、滴、漏”等现象。月初,5#炉作为容量最大的加热炉,由于使用频次高,台车台车架钢构烧损严重,导致上导轨变形,砌砖座烧损松动,浇注料大面积坍塌,严重影响了生产进度。分公司立即成立炉窑修理突击队,通过自行认真研究图纸,与同行业探讨,历时15天自行修理完毕,既避免了招标修理价格高、工期长的问题,同时节约修理费用30余万元。
在寻求产量突破的同时,技术创新也步履不停。分公司某重点用户主轴材料性能高,以往均采用99吨双真空钢锭,技术人员在吃透技术要求前提下,精准发力解决瓶颈问题,与冶炼车间共同开发使用72吨单真空钢锭并锻造成功,使得主材成本大幅下降,为市场开发奠定了坚实的基础。